História:
A balanceadora tem uma história de mais de 100 anos. Em 1866, a alemã Siemens inventou o gerador. Quatro anos depois, o canadense Henry Martinson patenteou a técnica de balanceamento, dando início à indústria. Em 1907, o Dr. Franz Lawaczek forneceu ao Sr. Carl Schenck técnicas aprimoradas de balanceamento e, em 1915, ele produziu a primeira máquina de balanceamento de dupla face. Até o final da década de 1940, todas as operações de balanceamento eram realizadas em equipamentos de balanceamento puramente mecânicos. A velocidade de balanceamento do rotor geralmente leva em consideração a velocidade de ressonância do sistema de vibração para maximizar a amplitude. Não é seguro medir o balanceamento do rotor dessa maneira. Com o desenvolvimento da tecnologia eletrônica e a popularização da teoria do balanceamento de rotor rígido, a maioria dos dispositivos de balanceamento adotou a tecnologia de medição eletrônica desde a década de 1950. A balanceadora de pneus com tecnologia de circuito de separação planar elimina efetivamente a interação entre os lados esquerdo e direito da peça de trabalho de balanceamento.
O sistema de medição elétrica passou pelas etapas de flash, wattímetro, digital e microcomputador, e finalmente surgiu a máquina de balanceamento automática. Com o desenvolvimento contínuo da produção, cada vez mais peças precisam ser balanceadas, quanto maior o tamanho do lote. A fim de melhorar a produtividade e as condições de trabalho, a automação do balanceamento foi estudada em muitos países industrializados já na década de 1950, e máquinas de balanceamento semiautomáticas e linhas automáticas de balanceamento dinâmico foram produzidas sucessivamente. Devido à necessidade de desenvolvimento da produção, nosso país começou a estudá-la passo a passo no final da década de 1950. Este é o primeiro passo na pesquisa de automação do balanceamento dinâmico em nosso país. No final da década de 1960, começamos a desenvolver nossa primeira linha automática de balanceamento dinâmico de virabrequim CNC de seis cilindros e, em 1970, produzimos com sucesso em testes. A tecnologia de controle por microprocessador da máquina de teste de balanceamento é uma das direções de desenvolvimento da tecnologia mundial de balanceamento dinâmico.
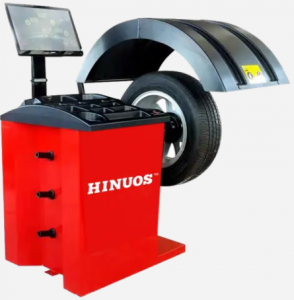
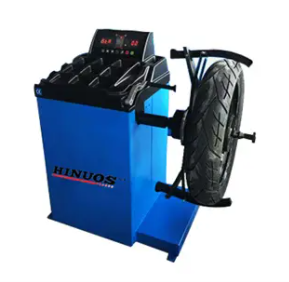
Tipo de gravidade:
O balanceador de gravidade é geralmente chamado de balanceador estático. Ele depende da gravidade do próprio rotor para medir o desequilíbrio estático. Ele é colocado nos dois rotores de guia horizontais, se houver um desequilíbrio, ele faz o eixo do rotor no momento de rolamento da guia, até que o desequilíbrio na posição mais baixa seja apenas estático. O rotor balanceado é colocado em um suporte apoiado por um mancal hidrostático, e um pedaço de espelho é embutido sob o suporte. Quando não há desequilíbrio no rotor, o feixe da fonte de luz é refletido por este espelho e projetado para a origem polar do indicador de desequilíbrio. Se houver desequilíbrio no rotor, o pedestal do rotor se inclinará sob a ação do momento de gravidade do desequilíbrio, e o refletor sob o pedestal também se inclinará e desviará o feixe de luz refletido, o ponto de luz que o feixe projeta no indicador de coordenadas polares deixa a origem.
Com base na posição coordenada da deflexão do ponto de luz, o tamanho e a posição do desequilíbrio podem ser obtidos. Em geral, o balanceamento do rotor inclui duas etapas: medição e correção do desequilíbrio. A máquina de balanceamento é usada principalmente para medição do desequilíbrio, e a correção do desequilíbrio é frequentemente auxiliada por outros equipamentos auxiliares, como furadeiras, fresadoras e máquinas de solda a ponto, ou manualmente. Algumas máquinas de balanceamento têm o calibrador como parte da máquina de balanceamento. O sinal detectado pelo pequeno sensor da rigidez do suporte do balanceador é proporcional ao deslocamento da vibração do suporte. Um balanceador de rolamento rígido é aquele cuja velocidade de balanceamento é menor que a frequência natural de um sistema de rolamento de rotor. Este balanceador tem uma grande rigidez, e o sinal detectado pelo sensor é proporcional à força de vibração do suporte.
Indicadores de desempenho:
A principal performance dobalanceadora de pneus é expresso por dois índices abrangentes: o desequilíbrio mínimo remanescente e a taxa de redução do desequilíbrio: a Unidade de Precisão de Balanceamento (G.CM), quanto menor o valor, maior a precisão; o período de medição do desequilíbrio também é um dos índices de desempenho, que afeta diretamente a eficiência da produção. Quanto menor o período de balanceamento, melhor.
Horário da publicação: 11/04/2023